RMC on track to save even more woodies
208 ReTrak latest innovation from pioneering company
Over time, the tracks on traditional wooden coasters deteriorate–more so than their steel counterparts. As park fans, you’ve likely endured your fair share of rough rides on woodies (and “rough” might be putting it charitably) through the years. To restore the coasters, parks have had to regularly re-track them, spending upwards of $50,000 to $100,000 annually on the Sisyphean task. That has typically involved ripping out the most problematic sections of track and rebuilding them on site.
Frustratingly, the restored tracks would sometimes get wonky again after just a couple of seasons of operation. In extreme cases, parks would throw their hands up in frustration and call it a day, razing their wooden coasters altogether.
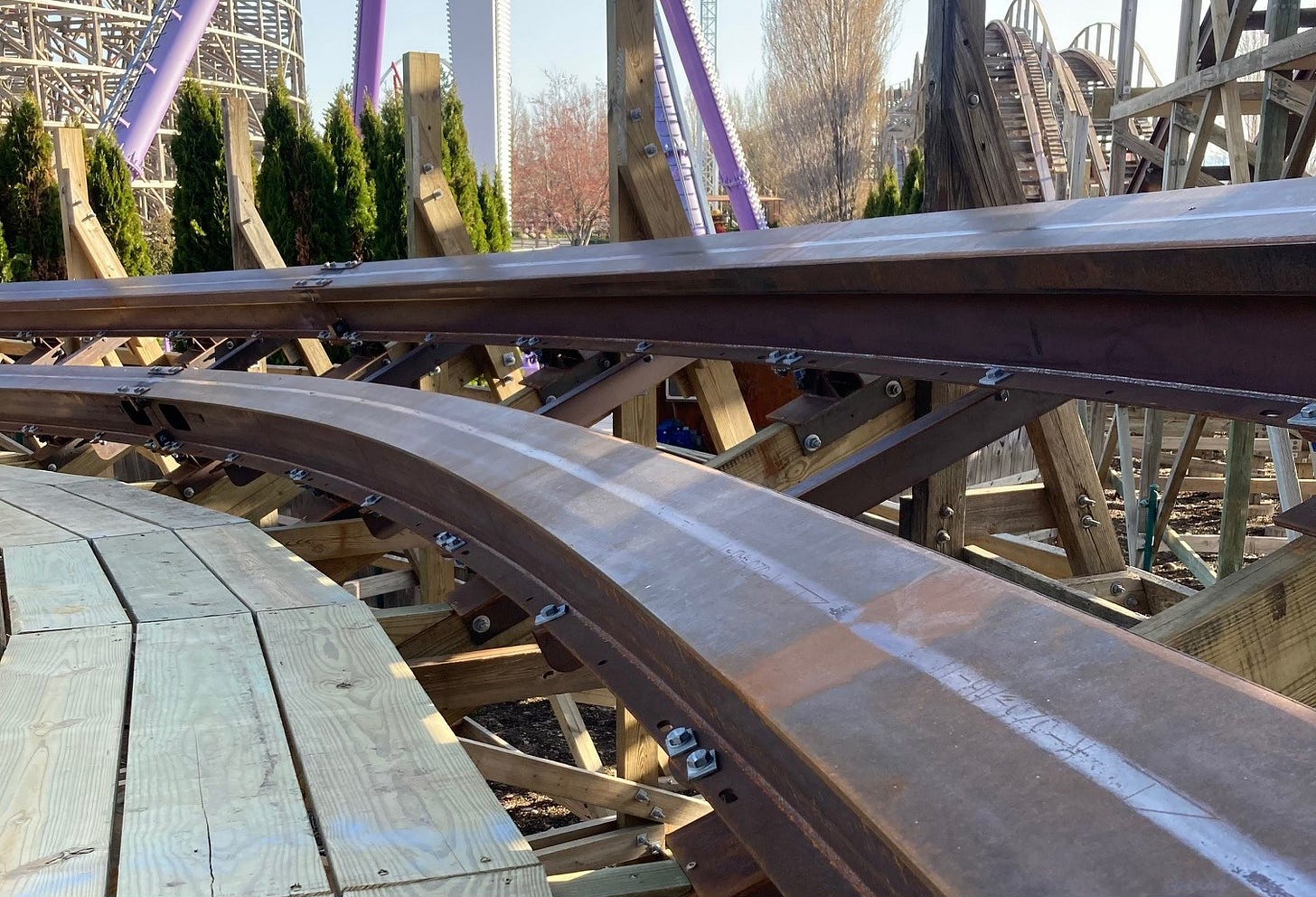
That was then. Now, some clever ride wranglers have developed newfangled alternatives to address the age-old problem. The latest to offer a solution are the coaster pioneers at Rocky Mountain Construction with their 208 ReTraK replacement track. (In case you’re wondering, “208” refers to the Idaho area code where the company is based.) Here’s the deal: Instead of swapping out punishing track sections with new, traditional wooden track (which includes stacks of wood topped with a thin metal rail on which the trains’ wheels run), RMC uses weathered steel track that is based on the company’s revolutionary I-Box track.
Wait a sec, you might be thinking. How is this any different from the hybrid wooden and steel coasters that RMC has been Frankensteining since 2011, such as Wildcat’s Revenge at Hersheypark? For those rides, the company has been re-profiling existing wooden coasters, often making them much taller, steeper, and faster, and adding new elements such as barrel rolls and zero-G stalls. For 208 ReTraK projects, RMC is just re-tracking rides and sticking with their established profiles. Also, while the coaster connoisseurs could replace entire tracks, most parks would only want them to replace sections at a time. In a sense, then, the resulting rides are true wooden-steel coaster hybrids with some track sections retaining their traditional wooden origins and other sections sporting all-steel track.
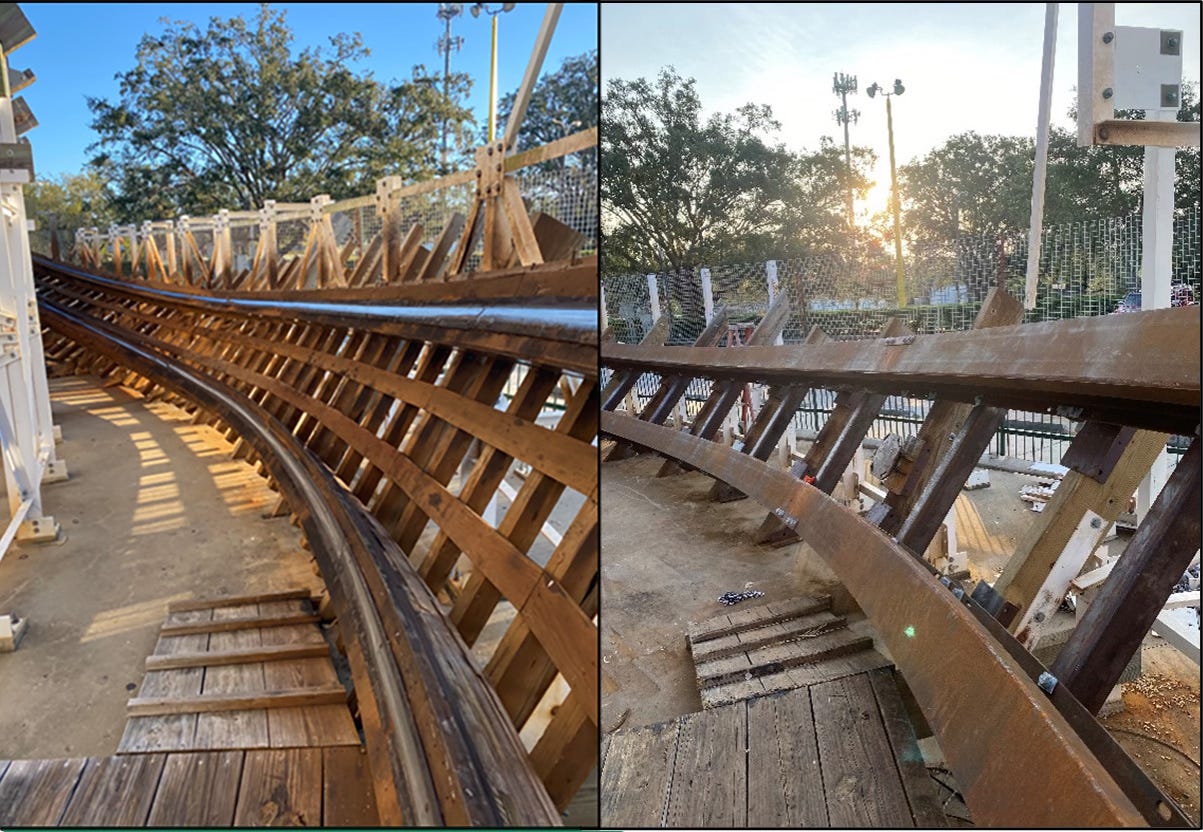
According to Tevin Hamilton business development and ride support specialist for RMC, the company might make minute adjustments to the original profile when necessary. He says that wooden tracks can sometimes get “rumble strippy” and cause trains and their passengers to shudder and vibrate as they tear through a course. To make the path as smooth as possible during re-tracking, the company might tweak the specs an inch or so in any direction.
RMC first applied 208 ReTraK to Timber Terror and Tremors, two coasters at Idaho’s Silverwood Theme Park, which is in the ride company’s 208 area code backyard. It subsequently worked its restoration magic on Mine Blower at Fun Spot America in Florida. Among the three coasters, it has replaced about 2,700 feet of track. Because the 208 product mimics wooden track, parks can continue to use the ride’s existing trains and controls, making it a “plug and play” option, says Hamilton.
What about the points where the original wooden track meets the new steel strack? The transitions need to be literally and figuratively seamless.
“We look for nice 1D sections,” Hamilton says, referring to track that is straight with no turns, rises, or banking (which would be “2D” or “3D” in coaster tech talk). “We’ll cut back the wood stacks and sew into that,” he adds. “It takes a bit of finesse.”
The result?
“If you’re not an enthusiast, you probably don’t even notice the transitions,” explains Hamilton. “Except that the coaster seems much smoother than before.”
Here is a POV ride on Silverwood’s Timber Terror shot in 2020, before RMC’s 208 ReTrak:
RMC is not the only company offering re-tracking solutions for wooden coasters. Great Coasters International offers the similar Titan Track, which is rivet-based and has no welds. The Gravity Group has an all-wood alternative with its precut vertical wooden track. RMC, however, may be able to lay special claim to the process.
After all, its I-Box track, which turned the coaster industry on its ear, was famously born out of the frustration that the company experienced when it re-tracked and repaired aging wooden coasters only to see them quickly fall back into disrepair. Thinking their had to be a better way, RMC’s owner and founder, Fred Grubb, and ride engineer and designer, Alan Schilke, had a brainstorming session in which they developed the hybrid wooden-steel I-Box concept. Now, the company has come full circle and returned to its roots by applying its I-Box breakthrough to re-tracking projects.
Hamilton says that by saving money on repairs and upkeep and reducing routine maintenance, 208 ReTraK offers great value for parks. From a fan’s perspective, however, RMC’s product delivers much smoother rides and helps preserve coasters that might otherwise fall to the wrecking ball. For that, it’s yet another reason to salute the innovative company.
What’s your take on 208 ReTrak? Are wooden coasters still woodies after some of their track is replaced with RMC’s replacement product? Have you experienced any of the coasters on which RMC has installed its 208 ReTrak? Do you have suggestions for coasters that could benefit from the new track?
Arthur, I appreciate your mix of articles including this one. I was able to share this with my busy daughter to quickly explain how and why this kind of track is used.